In today’s rapidly evolving manufacturing and engineering industries, the role of a CNC machinist stands out as both crucial and compelling. These professionals combine technical skill, precision, and innovation to shape the world around us, from creating vital components in aerospace to pioneering new products in the automotive sector. Given its importance, our journey to explore how to kickstart a career as a CNC machinist is not just timely; it’s essential. We aim to demystify the path to becoming a CNC machinist, understanding its significance in advancing technology and manufacturing.
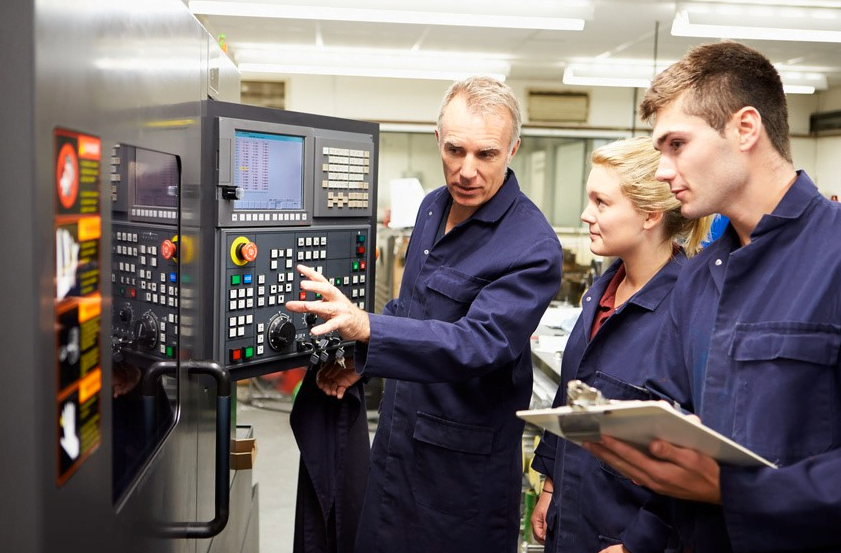
As we delve into this exploration, we’ll cover the foundational steps necessary to embark on this promising career. From understanding what a CNC machinist does—operating Computer Numerical Control machines that cut, shape, and finish metal and plastic parts—to navigating the myriads of training programs available, we’ve got it mapped out. Furthermore, we’ll provide a glimpse into the day-to-day life of a CNC machinist, examine the career outlook, discuss advancement opportunities, and consider the challenges and rewards that come with this profession. Join us as we outline the path to not just becoming a CNC machinist but excelling in this dynamic field.
What Is a CNC Machinist?
A CNC (Computer Numerical Control) machinist is a skilled professional who operates and programs machine tools such as lathes, mills, and grinders. These tools are controlled by computers and are essential for producing precision metal or plastic parts. The role of a CNC machinist is critical in various industries where high-quality, custom parts are required.
Definition and Overview
CNC machinists use blueprints, sketches, or computer-aided design (CAD) and manufacturing (CAM) files to create detailed and precise parts. They are responsible for setting up machines, writing and testing programs, and making necessary adjustments during the production process. Precision measuring instruments are often used to ensure that the completed parts meet all specified requirements.
Roles and Responsibilities
The primary responsibilities of a CNC machinist include:
- Examining and analyzing blueprints, sketches, and computer-related files to understand project specifications.
- Setting up and operating CNC tools to produce products according to precise specifications.
- Measuring and examining completed products to ensure they meet quality standards.
- Performing routine machine maintenance and making adjustments to optimize performance.
CNC machinists must possess strong mechanical and technical skills, expertise in math and computer applications, and manual dexterity. Their work often involves critical thinking and decision-making, especially when it comes to selecting appropriate machines and tools for specific jobs.
Industries Needing CNC Machinists
CNC machinists are vital in industries such as motor vehicle manufacturing, aerospace product manufacturing, mechanical engineering, and metalworking machinery manufacturing. These sectors demand high precision and often require custom parts, making the role of CNC machinists indispensable. The ability to quickly adapt to changes in production runs and specifications is crucial in meeting the diverse needs of these industries.
In summary, CNC machinists combine their knowledge of mechanical design, mathematics, and computer programming to operate sophisticated machinery that produces essential components across various sectors. Their expertise ensures that industries can maintain high production rates and standards of quality, making them a cornerstone of modern manufacturing.
Becoming a CNC Machinist
Embarking on a career as a CNC machinist involves a combination of education, hands-on training, and certification. We’ll explore the key steps to becoming skilled in this technical field.
Educational Requirements
To begin, a high school diploma or GED is essential for aspiring CNC machinists. Many individuals further their education by attending technical schools or community colleges, where they can focus on acquiring specific CNC skills. These educational programs typically cover a broad range of subjects including math, engineering, computer technology, and more. Importantly, courses on CAD/CAM operation and design technology are integral to these programs. While an associate degree is beneficial, it is not mandatory for entering the field.
Gaining Experience: From CNC Operator to Machinist
Gaining practical experience is crucial in the CNC machining field. Many machinists start their careers as CNC operators, gaining foundational skills before advancing. Trade schools often require apprenticeships, internships, or externships, providing valuable real-world experience. For those entering the field, companies may offer on-the-job training programs. It typically takes about four to five years of combined education and practical experience to become fully proficient as a CNC machinist.
Certification and Advancement
Certification plays a significant role in the career development of CNC machinists. Whether holding a degree or not, obtaining certifications such as those offered by the National Institute for Metalworking Skills (NIMS) can demonstrate a machinist’s proficiency. NIMS certifications assess skills in areas from entry-level programming and operation to advanced CNC milling and turning. These certifications are highly regarded by both professionals and employers and are instrumental in career advancement.
By following these structured steps—gaining the necessary education, accumulating hands-on experience, and earning relevant certifications—you can effectively prepare for a successful career as a CNC machinist.
CNC Machinist Training Programs
Types of Programs Available
CNC Machinist training programs vary in scope and duration, catering to different levels of expertise and career aspirations. At NASCAR Technical Institute, for instance, the CNC Machining Technology program is designed to be completed in as few as 36 weeks. This program equips students with the skills necessary to set up, operate, and troubleshoot CNC machines to ensure flawless part creation. Similarly, Goodwin University offers an 18-credit CNC certificate program that can be completed in just two semesters, and an accelerated certificate in CNC Machining, Metrology, and Manufacturing Technology, which spans 22.5 weeks full-time. For those looking for more comprehensive education, Goodwin also provides an associate degree in CNC machining, which takes less than two years to complete, with classes available in the evenings for added flexibility.
Skills Learned in Training
Throughout these training programs, students acquire a robust set of skills essential for a successful career as a CNC machinist. Key competencies include reading blueprints and utilizing CAD and CAM software programs, interpreting geometric dimensioning and tolerancing, and programming, setup, operation, and disassembly of CNC lathes and mills. Additionally, students learn to align, secure, and adjust workpieces and cutting tools, monitor machine movement and speed, and examine completed products for defects to conduct product testing. The training also emphasizes smoothing part or product surfaces and working with industry-preferred tools and technology from brands like Mastercam, Mitsubishi Materials, and Mitee-Bite Products LLC. Safety and job planning best practices form an integral part of the curriculum, preparing students for real-world manufacturing environments.
Benefits of Completing a Formal Training Program
Completing a formal CNC machinist training program offers numerous benefits. Graduates are well-prepared to apply for roles such as CNC programmer, CNC setup operator, and CNC operator, with potential career advancement to positions like quality control inspector and shop supervisor. Some may even choose to open their own CNC machinist businesses. Training programs like those offered at NASCAR Tech and Goodwin University prepare students to earn nationally-recognized, portable credentials from the Manufacturing Skill Standards Council (MSSC) and the National Institute for Metalworking Skills (NIMS). These credentials significantly enhance a machinist’s employability and are highly regarded in the industry. Moreover, the hands-on experience and technical skills gained through these programs increase job opportunities and potential earnings, making graduates stand out in the competitive job market.
The Day-to-Day Life of a CNC Machinist
As a CNC machinist, our daily responsibilities are diverse and require a blend of technical, mechanical, and problem-solving skills. Here, I’ll walk you through a typical day, focusing on our usual duties and tasks, the environment we work in, and the job satisfaction that comes with this role.
Typical Duties and Tasks
Our day typically begins with reviewing the production schedule and then moving on to the specific tasks at hand. These include:
- Examining and analyzing blueprints, sketches, and computer-related files to understand the specifications for each project.
- Setting up and operating CNC machines such as lathes, mills, and grinders, ensuring each piece is crafted according to precise requirements.
- Performing machine setups, which are crucial for ensuring accuracy and efficiency in our work. This involves adjusting the machine settings, loading tools, and positioning materials.
- Conducting quality checks using precision measuring instruments to ensure that each part meets the stringent specifications set out in the design plans.
- Documenting processes and outcomes, which helps in maintaining quality control and supports continuous improvement in our operations.
Throughout the day, I also engage in troubleshooting and maintenance tasks to ensure that all equipment operates at peak efficiency. This proactive approach helps minimize downtime and ensures consistent production quality.
Work Environment
The work environment for CNC machinists is dynamic and fast-paced but also requires a high level of precision and attention to detail. We operate in well-organized settings where safety is a top priority. Regular maintenance of the workspace and adherence to safety protocols are essential to prevent accidents and ensure a smooth workflow. The environment is typically noise-controlled, and we use personal protective equipment to safeguard against potential hazards.
Collaboration is also a key aspect of our work environment. We often work closely with teams, including engineers and other technicians, to refine machining processes and enhance output efficiency. This collaborative atmosphere not only helps in problem-solving but also fosters a sense of community and support among colleagues.
Job Satisfaction
Regarding job satisfaction, being a CNC machinist can be both challenging and rewarding. While the Career Explorer survey indicates that machinists rate their career happiness at 2.7 out of 5, it’s important to note that job satisfaction can vary widely based on individual experiences and workplace dynamics. Many of us find great satisfaction in the tangible results of our work—seeing a physical product take shape from raw materials is incredibly gratifying.
However, challenges such as the need for continuous learning and adaptation to new technologies can impact satisfaction levels. The ability to solve complex problems and the continuous improvement in skills can lead to a high level of personal and professional growth, which many find rewarding.
In conclusion, the day-to-day life of a CNC machinist involves a variety of tasks that require technical skills and problem-solving abilities. The work environment is structured and safety-focused, while job satisfaction can vary depending on various factors, including personal achievements and workplace conditions. As machinists, we play a critical role in manufacturing, contributing significantly to the creation of high-quality products.
Career Outlook for CNC Machinists
The job outlook for CNC machinists is promising, with the U.S. Bureau of Labor Statistics projecting a 3% job growth rate from 2020 to 2030. This growth is fueled by the increasing need for precision manufacturing across various industries, highlighting the importance of CNC machinists in today’s economy.
Job Growth and Demand
The demand for skilled CNC machinists is driven by the growing reliance on precision manufacturing in sectors such as aerospace, automotive, medical devices, and electronics. The shift from manual labour to automated systems has not only increased productivity and accuracy in manufacturing but also created new job opportunities for CNC machinists. Additionally, the integration of advanced technologies like robotics and artificial intelligence into manufacturing processes has expanded the scope of CNC machining jobs, requiring machinists who are proficient in these new technologies.
Industries Hiring CNC Machinists
CNC machinists play a crucial role in industries that demand high precision and custom parts. Key sectors that frequently seek skilled CNC machinists include motor vehicle manufacturing, aerospace product manufacturing, mechanical engineering, and metalworking machinery manufacturing. These industries rely on the specialized skills of CNC machinists to maintain high production rates and uphold strict quality standards.
Geographical Hotspots for CNC Machinists
The geographical distribution of CNC machinist jobs varies, with certain states offering more opportunities due to their industrial profiles. States like California, Texas, and Michigan are known for having the highest employment rates for machinists. Additionally, regions known for manufacturing, such as the Midwest and parts of the Northeast, continue to be vital areas for CNC machinists looking for employment. The availability of jobs often correlates with the presence of major manufacturing plants and the local economic conditions, influencing where machinists may find the best opportunities and potentially higher wages.
In sum, the career outlook for CNC machinists is robust, characterized by steady job growth, the necessity for advanced technical skills, and the geographical variances in job availability. As industries continue to evolve and adopt new technologies, the role of CNC machinists will remain indispensable in the manufacturing sector.
Advancing Your Career as a CNC Machinist
Advancing your career as a CNC machinist involves continuous learning and adapting to new technologies and roles within the industry. Here we explore several pathways that can help you grow professionally and achieve greater success in your field.
Continuing Education Opportunities
One of the most effective ways to advance in the CNC machining field is through continuing education. Participating in accredited training programs that offer Continuing Education Units (CEUs) is crucial. These units are often required for maintaining CNC certifications and are essential for staying updated with the latest machining practices. Programs like those offered by camInstructor provide in-depth Mastercam training, which is crucial for both novice and experienced CNC machinists aiming to enhance their skills.
Specializing in Advanced Technologies
To remain competitive and highly skilled in the CNC industry, specializing in advanced technologies is key. Embracing automation and mastering state-of-the-art equipment, such as the Makino 5 and 4 axis machines, can significantly boost your capability to produce high precision and complex machined parts. Advanced CNC Technologies, for instance, offers opportunities to work with cutting-edge tools that enhance speed, precision, and efficiency in machining processes.
Management and Supervisory Roles
For those looking to take a step beyond the technical aspects of CNC machining, moving into management and supervisory roles can be a rewarding progression. Transitioning into these roles involves not just a deep understanding of CNC operations but also acquiring skills in leadership and personnel management. Effective managers in the CNC field are those who have a strong technical background and are capable of mentoring and leading teams, optimizing workflow, and making strategic decisions that enhance production efficiency.
By focusing on these areas—continuing education, specialization in advanced technologies, and stepping into managerial roles—you can significantly enhance your career prospects and contribute more effectively to the evolving field of CNC machining.
Challenges and Rewards of Being a CNC Machinist
Being a CNC machinist involves a unique blend of challenges and rewards that make this career both demanding and fulfilling. From handling the technical complexities to experiencing the satisfaction of creating precise components, the role is a dynamic mix of hard work and gratifying results.
Overcoming Technical Challenges
The road to mastering CNC machining is paved with technical challenges that require both skill and perseverance. One significant hurdle is the continuous need to adapt to the evolving technology landscape. As we integrate more sophisticated software and hardware, staying updated with the latest advancements is crucial. For instance, the use of advanced programming techniques and selecting the right tool paths is essential for achieving optimal results. Challenges like machining complex parts demand a deep understanding of material properties and the appropriate application of cutting speeds and feed rates. Effective maintenance, including regular service inspections, plays a crucial role in overcoming obstacles that could lead to machine downtime or failures.
Innovation and Creativity in Machining
CNC machining is not just about following a set of instructions; it’s about leveraging creativity to solve problems and innovate. The ability to create intricate designs and work with a variety of materials opens up endless possibilities for innovation. From crafting bespoke automotive parts to designing specialized medical devices, the scope for creative input is vast. Utilizing CNC for various applications, such as creating intricate wooden sculptures or custom metal parts, emphasizes the role of creativity in this field. This aspect of the job is particularly rewarding as it allows machinists to see their ideas transform from digital designs into tangible products.
The Satisfaction of Precision Manufacturing
There’s a profound sense of satisfaction that comes from CNC machining. This satisfaction is largely derived from the precision and quality of the work produced. Achieving the tight tolerances required in industries like aerospace and automotive is no small feat and requires a meticulous approach to every detail of the machining process. The pride in seeing a perfectly finished part that meets all specifications cannot be overstated. Moreover, the role CNC machinists play in manufacturing critical components that impact various aspects of everyday life adds a layer of significance and fulfilment to their work.
In summary, the life of a CNC machinist is marked by the ongoing challenges of technical demands and the rewards that come from overcoming these challenges through innovation and precision. The balance of rigorous demands and the rewarding outcomes shapes the career into a continuously engaging and fulfilling journey.
Conclusion
Navigating the multifaceted pathway to becoming a CNC machinist offers an insightful glimpse into a career that melds technical prowess with creative innovation. Through the articulation of essential steps, from acquiring the foundational knowledge and skills in training programs to the continuous adaptation and mastery of new technologies, this article has underscored the indispensable role CNC machinists play in today’s manufacturing landscape. The significance of their contributions touches upon various industries, emphasizing the demand for precision and excellence in creating components that propel technological advancement and societal progress.
The journey of a CNC machinist is characterized by a constant interplay between overcoming technical challenges and reveling in the accomplishments of meticulous workmanship. It opens up a spectrum of opportunities for career advancement, from specialized roles involving cutting-edge equipment to leadership positions that leverage one’s expertise to mentor and guide teams. As the field continues to evolve, the emphasis on continued education and certification highlights the dynamic nature of this career. Engaging with this article not only provides a roadmap for aspiring machinists but also celebrates the blend of knowledge, skill, and creativity that defines the essence of being a CNC machinist.
FAQs
1. What are the initial steps to becoming a CNC machinist?
To begin a career as a CNC machinist, you should first complete your high school education or obtain a GED. It’s recommended to attend a trade school to acquire the necessary skills and knowledge through its program. Some machinists also pursue an associate degree, although this is often not a requirement by most employers.
2. How can someone enter the field of CNC machining without any prior experience?
If you lack experience, you can start in entry-level positions within manufacturing shops. Roles such as part deburring, machine loading and unloading, and basic machine operation provide essential experience that can serve as a foundation for a career in CNC machining.
3. What are the career advancement opportunities for a CNC machinist?
CNC machinists typically have several paths for career advancement. Many progress to become CNC programmers, while others may specialize as tool or die makers. Some advance into managerial or supervisory roles. Additionally, those with entrepreneurial skills often choose to start their own businesses after gaining sufficient industry experience.
4. What steps should I follow to start a career as a machinist?
To start a career as a machinist, complete a high school diploma or equivalent, then enrol in a postsecondary machinist program at a community college or technical school. Participating in an apprenticeship can provide hands-on experience, and pursuing industry certifications will further enhance your qualifications. Continuous education throughout your career is essential for growth and staying updated with industry advancements.
Leave a Comment